Bioimpresión de huesos y tejidos humanos
La medicina del futuro
Escribe Paola de Titto
Lic. Cs. de la Comunicación UBA
por Enlinea
Hoy la técnica de impresión 3D es capaz de aplicarse y adaptarse a sectores tan diversos como la industria, la medicina o el Arte; para fabricar puentes de acero impreso en 3D como en la ciudad de Ámsterdam o piezas clave de uso quirúrgico para reconstruír ojos, orejas, cráneos y huesos.
Implantes y prótesis personalizados
Desde hace muchos años la medicina utiliza prótesis para mejorar la salud de las personas; puntualmente para solucionar cuestiones de nacimiento, desgastes de la edad o consecuencias de accidentes. El objetivo es evidente; reemplazar estructuras faltantes en el cuerpo para devolverle funcionalidad, independencia y autonomía a las personas en sus diferentes actividades en la vida cotidiana.
En medicina desde hace ya varios años se han diseñado diversos tipos de elementos como prótesis flexibles, para aplicar en la columna vertebral y conservar el movimiento normal o preservar la estabilidad, pasivas; mioeléctricas o híbridas, para miembros superiores, cadera, rodilla, dentales.
En la actualidad el avance tecnológico ha permitido una multiplicidad de desarrollos. Hoy tanto el diseño como los materiales surgen de impresoras 3D que, al combinarlos con células humanas, permiten como resultado innovadores procedimientos quirúrgicos en la medicina. Así, en las prácticas médicas la bioimpresión aporta múltiples beneficios y nuevas posibilidades:
Personalización de implantes, prótesis, injertos y elementos ortopédicos.
Reducción de costos en tratamientos.
Planificación quirúrgica mejorada.
Potenciar el avance en ingeniería de tejidos.
Caso real
A principios del mes de junio de este año se hizo público el trasplante de una oreja impresa en 3D con células humanas. La pieza 3D, creada por la empresa 3DBio Therapeutics encargada de medicina regenerativa en Queens/EUA, fue implantada a una joven paciente que nació con microtia; un defecto que hace que la aurícula sea pequeña y mal formada.
En el proceso de fabricación de impresión 3D se creó un objeto tridimensional sólido, siempre a partir de modelos digitales, al que se le sumó células formadoras del tejido cartilaginoso extraído de la oreja deformada; para generar así el crecimiento de millones de células nuevas para mezclar con “bio-tinta” a base de colágeno. Y como por arte de magia esa mezcla de colágeno, insertada en la bioimpresora 3D, fue tomando forma hasta asemejarse a la oreja de la paciente.
El aspecto final se logró al implantar la oreja de impresión 3D debajo de la piel y brindar una apariencia de nueva oreja. Así mismo, la comunidad científica a cargo de la creación e implantación difundió que los tejidos de la paciente continuarán regenerando el tejido del cartílago hasta exhibir una apariencia de oreja natural.
CNEA
El laboratorio del Centro Atómico Ezeiza, equipado para el cultivo celular, desarrolla biomateriales biocompatibles para fabricar implantes óseos más económicos y accesibles con características mecánicas similares a las del hueso a reemplazar, y filamentos de biomateriales para conseguir impresiones 3D y su aplicación en ingeniería de tejidos.
Investigación y desarrollo de modelado
Desde 2014 con la creación del Laboratorio Universitario de Tecnologías Adictivas aplicadas a implantes fabricados con impresión 3D el Hospital de Clínicas “José de San Martín” de la Universidad de Buenos Aires ha implantado impresiones 3D a medida de titanio y trabecular en deformidades de columnas, defectos acetabulares de cadera, defectos de huesos largos (por traumatismos u osteomielitis), defectos tumorales, fracturas complejas, corrección de deformidades óseas o secuelas de fractura.
Julio Honorio Pueyrredón, Jefe de la División de Ortopedia y Traumatología del Hospital de Clínicas, en diálogo con esta redacción comentó que “los implantes 3D de titanio trabecular a medida presentan una alta integración con los tejidos humanos ya que el titanio es un metal biocompatible y la disposición trabecular porosa con la que se fabrica aporta una estructura que permite el crecimiento del tejido óseo en su interior”.
A través de la impresión de modelos anatómicos, en casos y problemas concretos, la tecnología 3D aplicada en ortopedia y traumatología ha permitido no sólo estudiar y comprender mejor las dificultades que presenta cada caso sino también desarrollar implantes 3D anatómicos a medida para cada paciente. Diseñar guías e instrumental específico para su colocación y ensayar las prácticas de las operaciones previamente. Los resultados y avances son evidentes al simplificar cada ejecución; y también al disminuir la necesidad de injertos socios masivos de banco, sus posibles complicaciones y al acortar los tiempos quirúrgicos. “Otra ventaja es que al contar con impresoras 3D de metal en nuestro país los costos de los implantes impresos a medida han disminuido notablemente en comparación con los productos ofrecidos en catálogos comerciales” agrega el Dr. Pueyrredón.
“La impresión 3D aplicada a ortopedia y traumatología emerge como una tecnología revolucionaria y disruptiva que vino a cambiar el paradigma reglado (con soluciones limitadas de productos catalogados) por un nuevo paradigma donde el tratamiento ortopédico personalizado concilia la indicación, el estudio de la complejidad de cada caso y la planificación preoperatoria con el desarrollo de modelos anatómicos, instrumental especial e implantes anatómicos a medida de cada paciente” JHP.
Impresión 3D en el ámbito de la salud humana
Por DI. Tomás Benasso
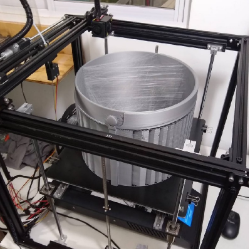
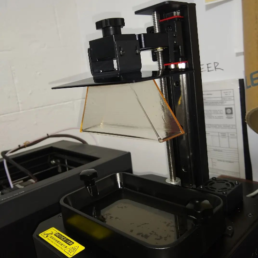
PH. Procesos de FDM y MSLA del taller de prototipos de la Carrera de Diseño Industrial de la FADU
La integración de los sistemas CAD-CAM-CAE (Diseño, Manufactura e Ingeniería Asistidos por Computadora) se ha dado en la industria desde la década de 1980, en especial y en sus orígenes en las grandes empresas aeronáuticas y automotrices. Con el paso del tiempo y el desarrollo de las tecnologías asociadas a estos procesos, esta integración se ha dado en todas las ramas y escalas de la industria manufacturera. Las ventajas competitivas que representa su utilización, sobre todo en la etapa de desarrollo de nuevos productos, es notable, y su acceso ha permitido procesos mucho más rápidos, económicos y seguros.
En particular las técnicas de RP (Rapid Prototyping) se han divulgado hasta niveles hogareños en lo que conocemos como impresión 3D y que es un claro paso adelante en la fabricación digital. El cambio de ciertos procesos de fabricación convencional o “sustractiva” por arranque de viruta (perforado, torneado, fresado, etc.) hacia procesos de manufactura digital o “aditiva” es un claro pilar de lo que se conoce como industria 4.0 o cuarta revolución industrial. Un nuevo paradigma de la gestión industrial en donde entre cimientos como la robótica colaborativa, soluciones ciberfísicas, la realidad virtual o aumentada, el BigData y el acceso a la nube (más los elementos antes mencionados) están permitiendo un nuevo modo de concebir a la industria contemporánea. Mucho más ágil respecto de los cambios, descentralizada e innovadora.
De los muchos procesos de fabricación aditiva que se han desarrollado en las últimas décadas; (en 1986 el ingeniero físico estadounidense Chuck Hull patentó el primer método y equipo para realizar objetos sólidos mediante impresión sucesiva de finas capas de un material que se endurece por polimerización mediante la exposición a luz ultravioleta, la estereolitografía SLA); la “impresión 3D” más popularizada ha sido el proceso conocido como FDM (Modelado por Deposición Fundida y últimamente la tecnología conocida como MSLA (Masked Stereolithography). En el primer caso un filamento plástico es fundido en un cabezal térmico y depositado sobre una cama de impresión, en el segundo una resina sintética es endurecida por luz ultravioleta dentro de una batea de impresión, y en ambos casos un software específico controla a la “impresora” que va depositando capa por capa (de 3 décimas de milímetro a 50 micrones) para ir conformando cualquier tipo pieza.
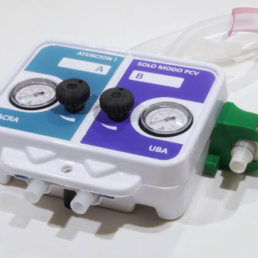
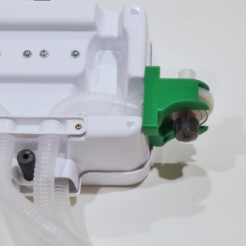
Entre los múltiples campos de aplicación en donde estas tecnologías han hecho un gran aporte, más allá del diseño industrial, la salud humana aparece como uno de los más interesantes. Aunque parezca ciencia ficción se está trabajando desde la “impresión” de órganos con materiales biológicos, aplicaciones protésicas y de implantes, y modelos de estudio para que equipos de médicos ensayen cirugías complejas antes de intervenir en el paciente.
En estos casos, y ya que cada individuo es morfológicamente diferente, la tecnología de fabricación aditiva se complementa con el escaneo 3D y la realidad aumentada. En la actualidad se utilizan métodos de impresión 3D de partes del cuerpo humano (o animal) utilizando imágenes de tomografía computarizada u otro proceso de escaneo, lo que permite realizar réplicas de secciones corporales. Estos modelos, reales y tangibles, que conservan las proporciones, las relaciones topográficas, la morfología y hasta el color, sin peligro de descomposición ni contaminación representan grandes herramientas en la docencia de la medicina y también como elementos de entrenamiento para equipos de cirugía, sobre todo las complejas y las de implantología.
Paralelamente, en la última década se han ido desarrollando distintos materiales biocompatibles para las distintas tecnologías de impresión arriba mencionadas, los mismos han sido aprobados por los correspondientes organismos de control y además se han hecho cada vez más accesibles respecto de su precio. Todo esto ha promovido otros tantos usos dentro del campo de la salud como ser la odontología. Aquí nuevamente la velocidad y valor económico en el proceso de desarrollo de una solución es muy importante y la impresión 3D se ha convertido en una técnica muy aplicada. Los mecánicos dentales pueden tener un modelo de una dentadura en pocas horas y trabajar sobre ella para ajustar implantes o fabricar placas de descanso sin someter al paciente a molestas maniobras sobre su boca. Gran parte de los profesionales de este sector se están especializando en las técnicas de escaneo e impresión 3D.
Otro ejemplo ligado a la salud, y solucionado gracias a la impresión 3D fue la fabricación descentralizada de las máscaras faciales que protegían a los profesionales de la salud en las primeras semanas de la pandemia del coronavirus. Dada la explosión de contagios, la demanda de estas protecciones en el mundo se elevó a una velocidad que la industria convencional no pudo responder. Aquí nuevamente la fabricación aditiva y descentralizada, junto con el poder de la nube, dieron respuesta a través del aporte de miles de “Makers” que alrededor del mundo compartieron archivos y se pusieron a fabricar y distribuir dichas máscaras en un tiempo récord. En un par de meses la industria convencional desarrolló la matricería y se hizo cargo de la oferta masiva, pero en un primer momento de crisis este nuevo paradigma dio claras señales de su potencialidad.
Para la misma época, en nuestro Taller de Prototipos de Diseño Industrial de la Facultad de Arquitectura y Diseño de Urbanismo de la UBA, se diseñó y fabricó una preserie de veinte “bifurcadores” de respiradores artificiales. El proyecto ACRA desarrollado por ingenieros y médicos de nuestra universidad, tomó forma y fue fabricado con apoyo de la impresión 3D. Parte de la matricería para termoformado, piezas mecánicas y válvulas antirretorno fueron fabricadas digitalmente en tiempo récord. El dispositivo permitiría conectar a dos pacientes, en lugar de uno, a un respirador artificial si el sistema de salud colapsaba. Nuevamente, además de la aceleración en el proceso de desarrollo, la impresión 3D permitió fabricar, por ejemplo, válvulas aéreas cuya distribución también había colapsado mundialmente.
Te puede interesar
ICON
House Zero, un nuevo proyecto sostenible
Iris van Herpen
Tecnología en la colección de la diseñadora Holandesa
Medicina
Modelos de placas y prótesis